Luvata Pori - integrated copper production with Rockwell Automation
Luvata Pori Oy transitioned to integrated Rockwell production automation. Luvata's production lines and machines are highly automated. Separate automation solutions were desired to be consolidated into one system in order to improve production manageability and usability.
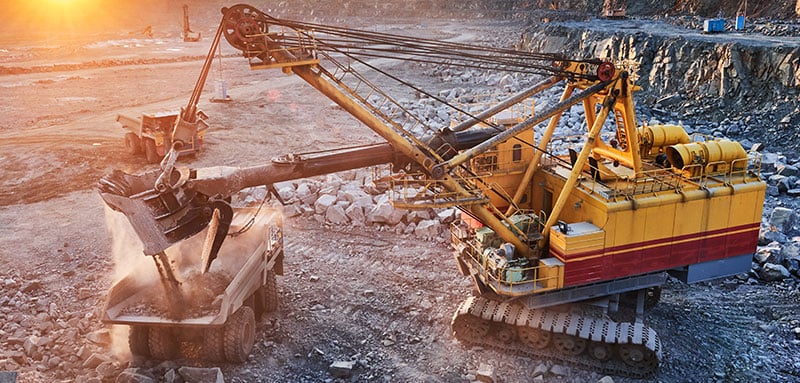
Luvata project in a nutshell:
Luvata Pori Oy, a major copper product manufacturer in Western Finland, produces over 40,000 tons annually, with 90% exported. To improve production efficiency and manageability, Luvata unified its previously separate automation systems using Rockwell Automation's Integrated Architecture.
This included CompactLogix and ControlLogix controllers, PowerFlex drives, and operator interfaces, all connected via an Ethernet/IP network. The new system enables centralized real-time control, scalable expansion, efficient data collection, and streamlined maintenance.
Solution was implemented in under six months.
Five key customer benefits:
-
Unified Automation System: Consolidating separate systems into Rockwell’s Integrated Architecture improved manageability and usability across all production lines.
-
Improved Connectivity and Data Handling: Centralized automation enhanced data collection, reporting, and machine connectivity, enabling better insights and decision-making.
-
Optimized Production Efficiency: Tailored automation solutions for each machine and line led to more efficient operations and easier maintenance.
-
Faster Implementation: Completed swiftly using Rockwell’s design tool library, with commissioning finalized in just one weekend—minimizing production downtime.
-
Scalability and Standardization: A single, standardized automation platform simplifies future upgrades, staff training, and system expansion.
Automated copper production for industry
Luvata's production lines and machines are highly automated. The goal was to combine separate automation solutions into one system to improve production manageability and usability.
Rockwell's Integrated Architecture automation product family was selected as the new comprehensive automation solution for Luvata Pori factory. It combines line automations based on CompactLogix and ControlLogix logic with other Rockwell automation products into one system.
The same system can also incorporate Rockwell's PowerFlex frequency converters and various Rockwell operator interfaces and reporting solutions.
The control and reporting of each machine and line were optimized by specifying and installing suitable automation solutions for each application, and later applications were combined into one Integrated Automation concept.
Using Rockwell's Integrated Automation design tool library, the project was completed in less than 6 months, with the actual commissioning taking place over a single weekend.